Kaizen
Applying rapid improvement processes to a manufacturing workplace can often be challenging for workers and leaders. During this course, participants gain a thorough introduction to the basics of Lean Enterprise thinking and the Kaizen methodology, and utilize their rapid improvement knowledge by responding to various operational issues within their organization.
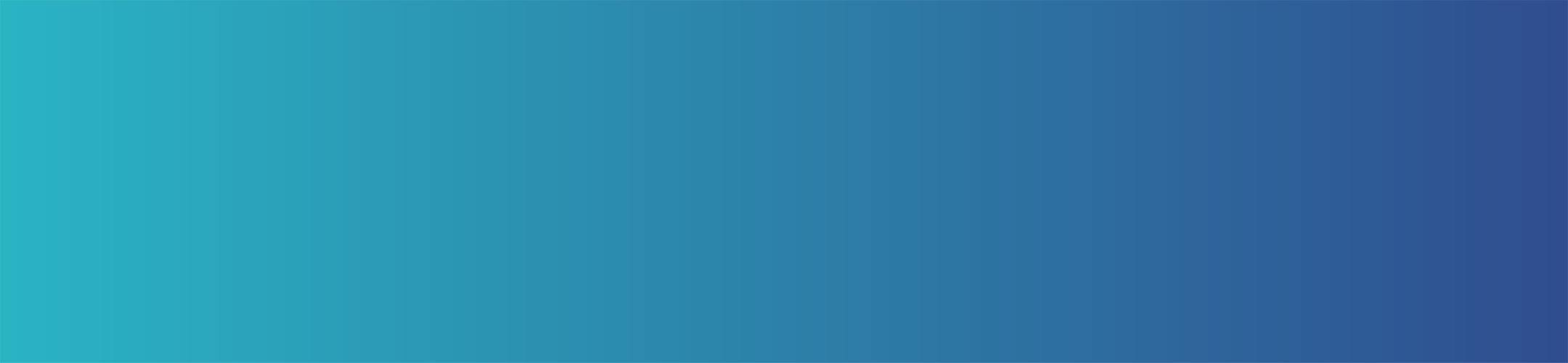
Course Summary:
Applying rapid improvement processes to a currently-operating manufacturing workplace can often seem like an insurmountable challenge for employees and leaders alike. To help workers overcome these obstacles, this five-day implementation event thoroughly immerses participants in a complete rapid improvement project, providing them with a corporate goal to achieve in less than a week’s time.
Within tight-knit teams, participants will gain a thorough introduction to the basics of Lean Enterprise thinking, the Kaizen improvement methodology, and a vast array of assorted development strategies, and will utilize their knowledge by responding to a number of operational issues within their organization. This intensive rapid improvement session is the ideal way to stoke your workforce’s creativity, flexibility, motivation, and problem-solving skills!
Discussed Topics:
- Understanding the Lean Enterprise and Kaizen processes.
- Guided facilitation through workplace improvement processes.
- Analyzing, discussing, and implementing a culture of continuous improvement in a manufacturing organization.
- The importance of acknowledging contributions to continuous improvement processes and solution application.
- Evaluating process improvements by examining quantifiable returns-on-investment.
Course Outline:
- Introduction to Lean Enterprise and Kaizen methodologies.
- Basic Lean Enterprise and Kaizen training.
- Observation and documentation of operational issues within participants’ workplaces.
- Issue prioritization and analysis.
- Solution-brainstorming sessions.
- Implementation of solutions into the existing processes of participants’ organizations.
- Final evaluations and course conclusion.
DURATION: Five (5) Day-Long Sessions
LEARNING ENVIRONMENT: In-Person Classroom and Participant Worksites
SCHEDULE: Please contact Amy Edwards, EMC’s Training Manager, at 1-866-323-4362 for more information.
Training is available in English.