Are you underestimating the TRUE value of ergonomics?
The True Value of Ergonomics - What Cost : Benefit To Expect?
Our experience tells us that most employers and businesses do not understand the true value that effective ergonomic initiatives can have on their bottom line.
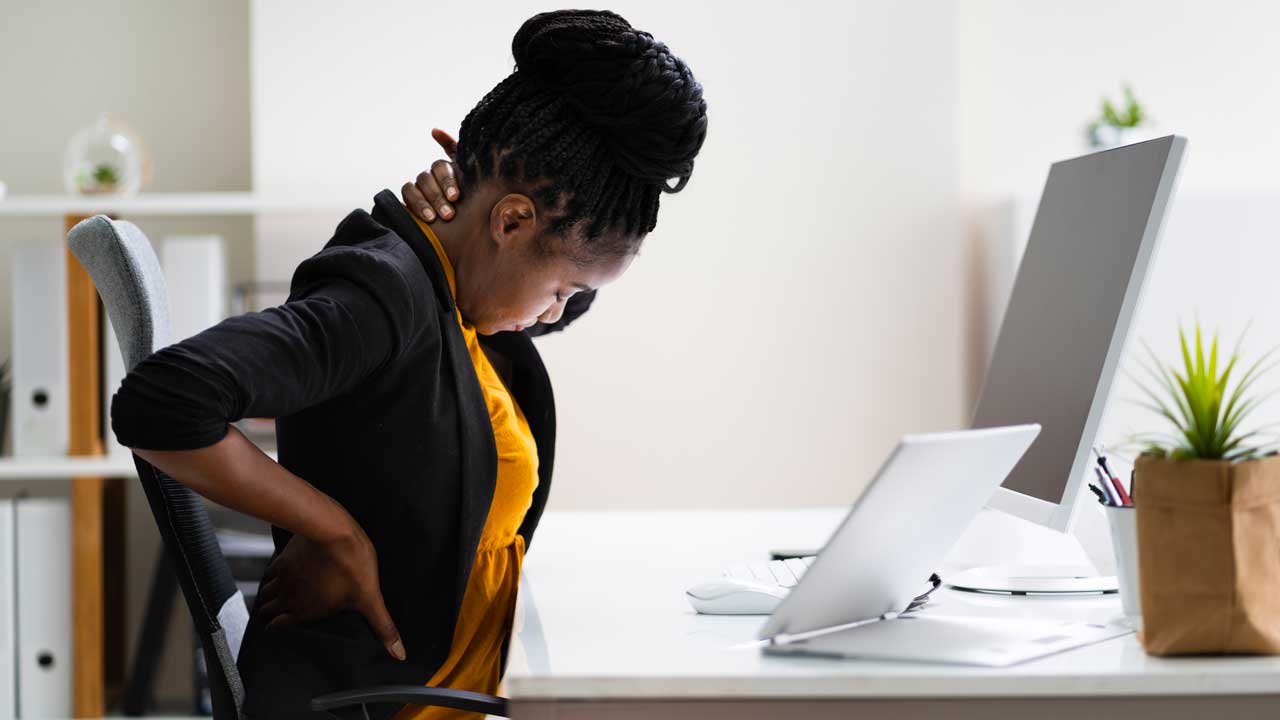
Are you underestimating the TRUE value of ergonomics? Our experience tells us that most employers and businesses do not understand the true value that effective ergonomic initiatives can have on their bottom line.
For too long ergonomics has resided in peoples’ opinion as just one component of a Health & Safety Program. Not only that, ergonomics is sometimes seen as a less “risky” or imminent health and safety concern, since ergonomics focuses on the cumulative effects of work on long-term health and well-being. As a result, ergonomics is not always prioritized, and the potential value of the program may not be fully apparent to all stakeholders. However, much like a good Health & Safety Program does more than ensuring employees’ safety, ergonomics provides many more benefits than injury prevention.
Research has shown that a good Ergonomics Program has the potential to improve productivity, reduce absenteeism, decrease quality issues and rework, and improve overall employee engagement. If we truly want Ergonomics Programs to be embraced by those outside the Health and Safety profession i.e. production & upper management, then we should start talking about ergonomics in their terms, in a language that appeals and speaks value to these groups.
Injury Cost Gains
In 2000, Ergonomists from the Washington State Department of Labor and Industries looked at 63 studies on Ergonomics Programs, and determined that workplace ergonomics interventions resulted in an average reduction in the number of musculoskeletal disorders by 50%, a reduction in lost time days by 65%, and a reduction in claim costs by 44%. While these numbers are impressive, they still only looked at the potential for gains resulting from injury cost reduction.
Gains from Reducing Absenteeism
One of the most thorough, and commonly referenced, studies on the effectiveness of ergonomics interventions was by Goggins et. al. (2008). This study reviewed over 250 case studies, including studies of large-scale Ergonomics Programs, as well as individual ergonomic improvements. In addition to the injury reduction benefits (59% decrease in number of MSD injuries, 75% reduction in lost workdays, and 68% reduction in claims costs), the study quantifies the average benefits of other business indicators.
The study found an average decrease in turnover of 48% and of absenteeism by 58%. The dollar value of reducing turnover and absenteeism cannot be underestimated. The average cost to replace an employee is commonly estimated to be ~16-20% of their annual salary, for entry level to mid level positions. The cost of a 3-day absence for an Engineer is estimated to be 154% of their wages, indicating that the employer is paying 54% on top of the employee’s wages while they are absent. Estimates of the absence cost for more manual labour positions are ~132% (Nicholson et. al., 2006). These potential gains would be most understood by a Human Resources department.
Gains from Reducing Scrap and Improvements in Productivity
The Goggins study also found a 67% decrease in scrap and errors, a benefit most noticeable by a Quality Assurance department. Finally, the study found a 25% increase in productivity and a 43% decrease in labour costs. One of the challenges is that ergonomics improvements may impact so many different departments and aspects of the organization, but individual improvements are often small enough to go unnoticed if not being tracked intentionally. Furthermore, each department often functions independently, so that the cumulative, and more substantial gains of an Ergonomic Program may not be fully realized.
Cost:Benefit
We continue to notice that there is a perception in some organizations that an Ergonomics Program costs money, and that the potential risk of an injury at some undetermined time in the future is not a strong enough driver. However, the Goggins study found an average cost:benefit ratio of 1:19 and a median cost benefit ratio of 1:6. In practice, that means that for every $1 put into interventions, the company should see a benefit of $6 – $19. When $50,000 is invested in an “Ergonomics Program” the company should see a return on investment of $300,000 – $935,000. When these ratios are calculated specifically for office ergonomics interventions, the average cost-benefit ratio was 1:1.8. In practice, a $500 investment on a good quality office chair should provide a return of $890!
One case study followed a Participatory Ergonomics Program in a textile factory (Tompa et. al, 2013). Over 4 years, the cost of the Ergonomics Program was calculated to be $65,787, which included training, ergonomics consulting, implemented changes, and production downtime. The findings showed a 65% decrease in first-aid, a 50% decrease in modified duties, decreased absenteeism by 23%, decreased LTD by 75%, and a small increase in production. The calculated savings of the Program, after the cost of the Program was accounted for was $294,825, with a cost benefit ratio of 1:5.5.
Take-Away Messages
- We should stop tying Ergonomics only to the prevalence of musculoskeletal disorders.
- We should speak the language of our audience.
- We should do a better job tracking data on the impact of initiatives across various departments.
If you would like assistance with your Ergonomics Program, Ergonomic Assessments, Office Ergonomics or Ergonomics Training contact ERGO Inc. today.